A while back a regular customer and friend of the Ti Cycles shop who has an appreciation for great bikes found himself in possession of a vintage road frame set from a noteworthy American builder that was nothing short of eye-catching.
photos courtesy of Scott Ebert
The “S-22” is a spot-on period piece from when it was built, in 1989, by a journeyman bike fabricator during the halcyon days of the modern US bike boom. The bike was bright as heck and highlighted by a retro-futuristic font and graphic scheme that would look equally at home in The Jetsons or The Flintstones. The striking orange, once full flourescent, had some dramatic fading but even that was pretty cool, adding rather than subtracting from the overall look.
The builder, David Tesch, is as interesting as the bike; a few breadcrumbs of information online has him popping up at a couple of important places during the the genesis of the modern American bike industry.
Tesch got his start in the right place at the right time, landing at the nascent Trek Bicycle Corporation just as it was transitioning from a small Wisconsin upstart making their TX series touring frames out of a rented warehouse to a full fledged bike manufacturer with a professional level line of road racing frames and a newborn MTB series. After a few years in Waterloo Tesch made his way out to California where he built frames for Specialized and Masi while also developing his own eponymous brand.
The frame wound up at Ti Cycles, having passed through eBay and at least a couple of owners, with a damaged chain stay in need of repair. At some point in its life a wider than appropriate rear hub had been used without properly respacing the frame and now a crack ran visibly across the inside face of the non-drive-side chain stay, just aft of the bridge.
photo courtesy of Scott Ebert
The frame’s visuals were so fetching that the Tesch looked stellar from 6 feet away. Up close it had a few blemishes befitting a 30-year old race bike, but since a proper repair meant that the paint had to come off nothing was lost.
Once it was stripped down to the bare True Temper and brass we found a few crusty corners and eventually a corresponding crack in the drive-side chain stay; a double stayectomy was in order. Before resurrecting the rear triangle we had to find the appropriate replacement parts; two identical pieces of steel frame tubing with the correct taper, the correct wall thickness, and two significantly different diameters at either end. It took a while but eventually Dave tracked down the ideal material and went to work.
After a lot of tedious pressing, cutting, grinding, filing, sanding, and maybe a little bit of swearing, this time capsule was brought back into top form, straight as an arrow with two new chain stays, a rear dropout alignment and re-spacing, and scoured clean inside and out to prep for fresh paint.
We handed the frame and fork over to the color wizards at Black Magic Paint for a museum quality restoration, and the finished product does not disappoint.
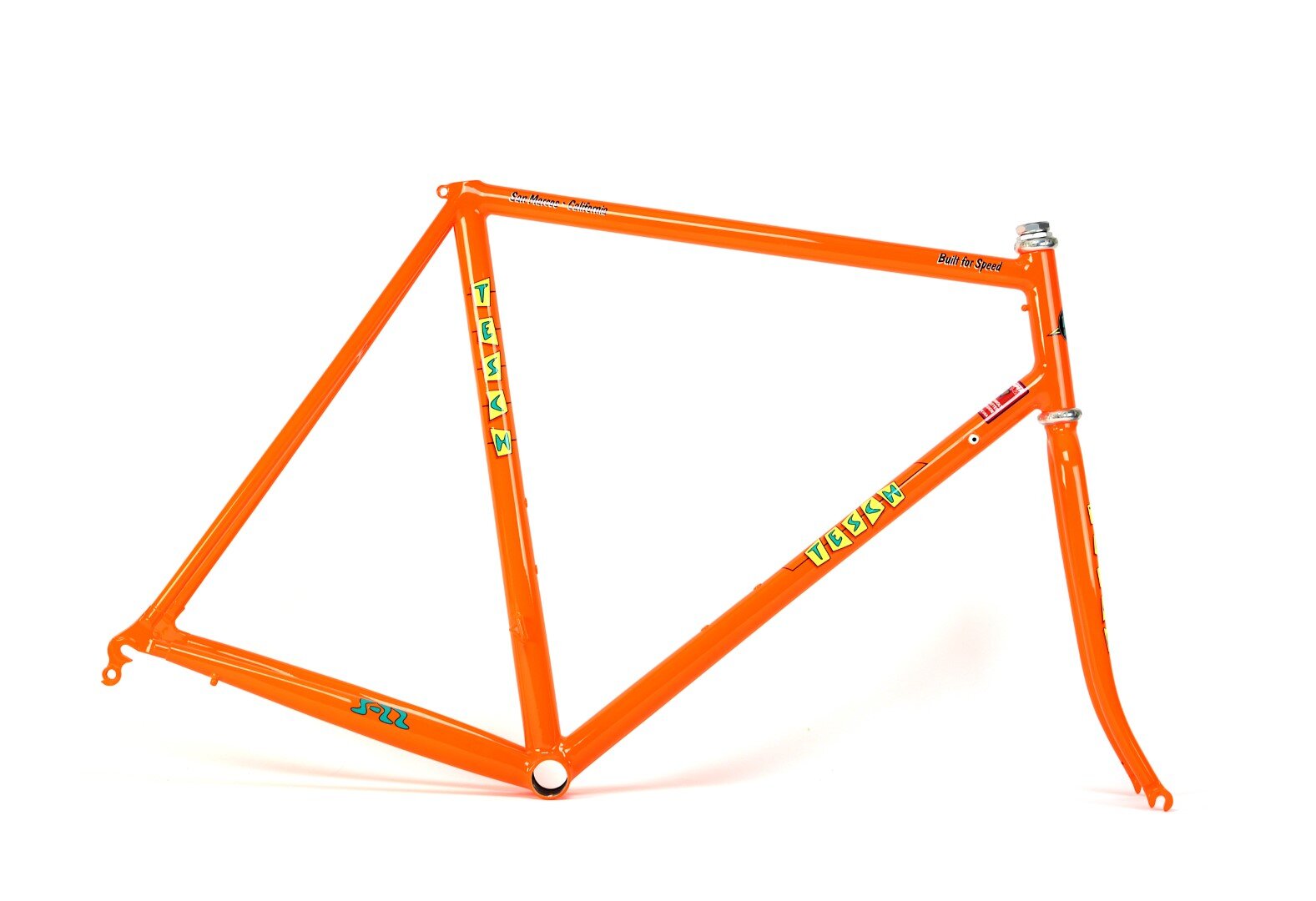
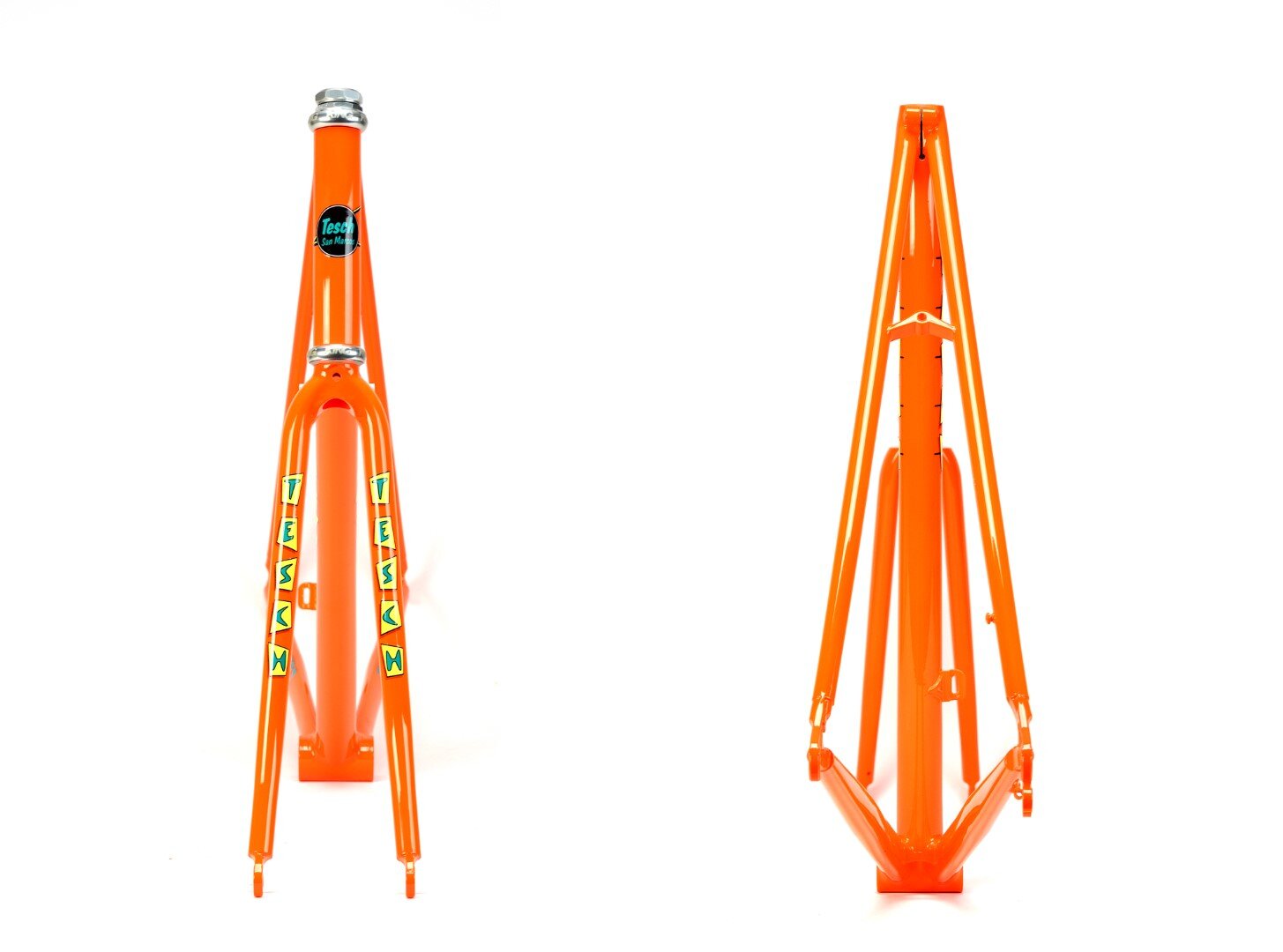
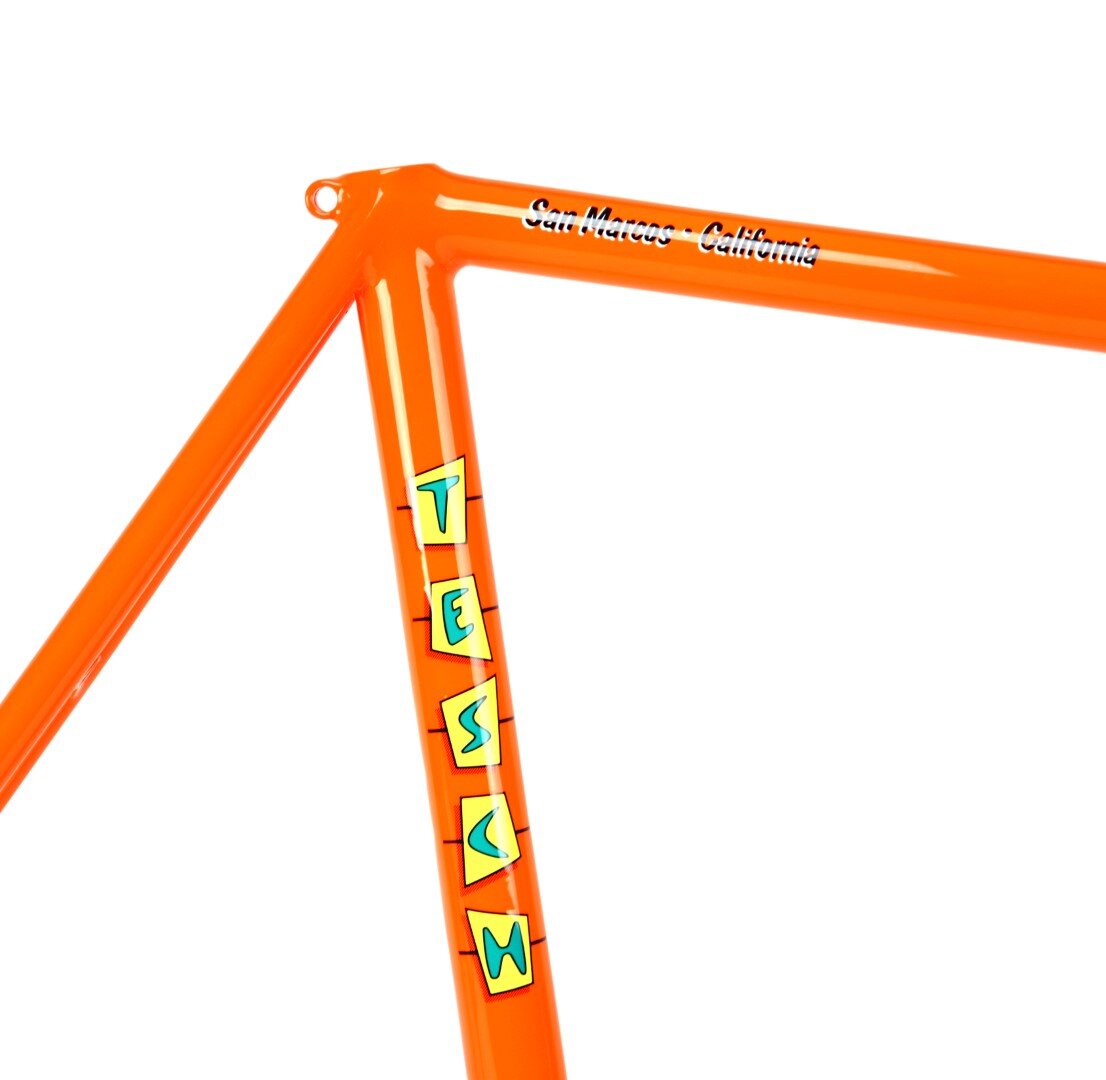

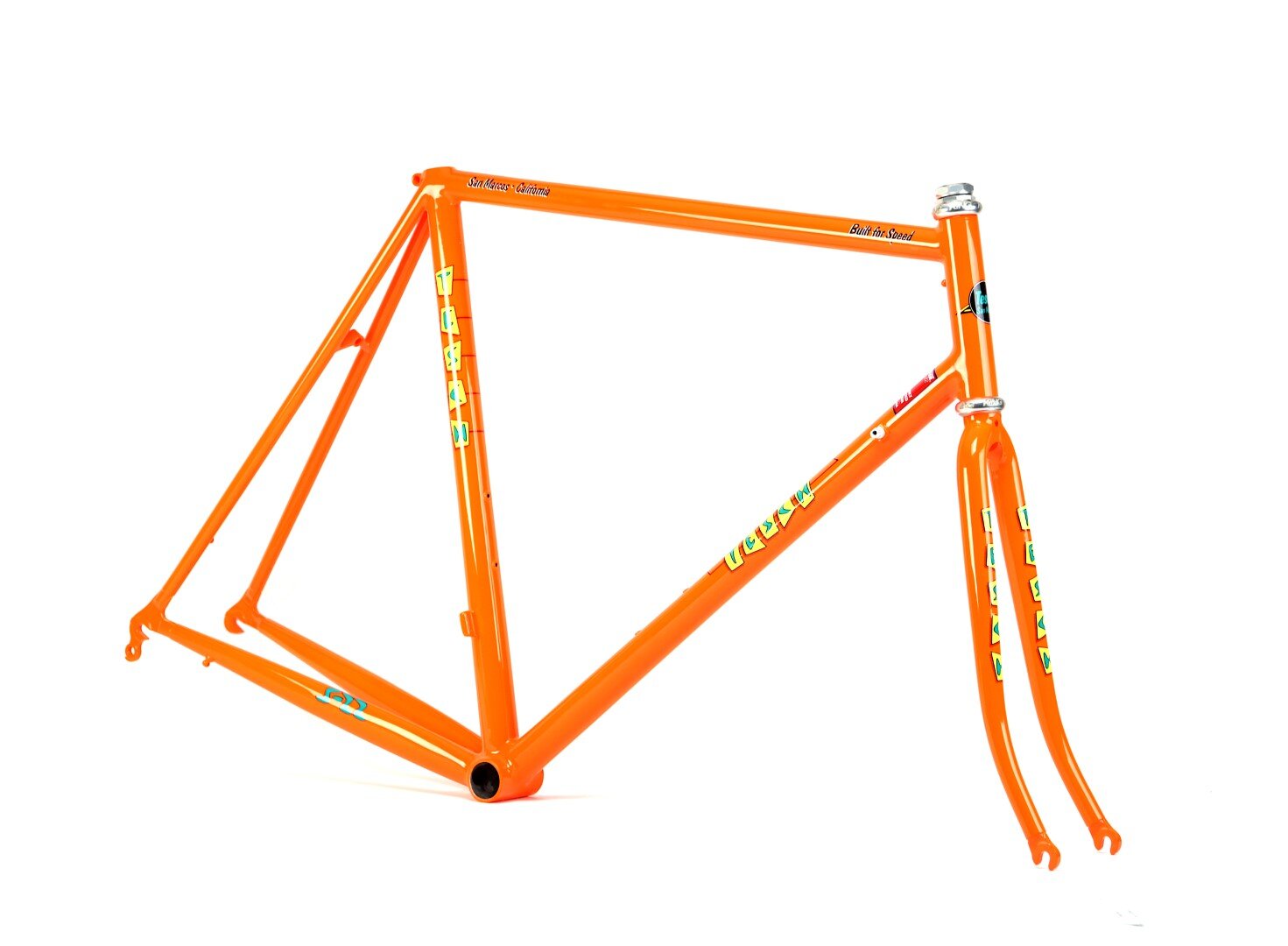

More information on Tesch bikes can be found at ClassicRendezvous.com